Top-Class Tin Can Manufacturing Brand
We are a specialized can manufacturing company with a firm belief in offering quality two-piece cans or three piece cans for fish, fruits, vegetables and pet food. With 11 fully automated lid- and can-making production lines, our company has continuously introduced advanced tin cans and canned food over the years.
5,000 ㎡Factory
12+4Production lines
40+Employees
Our Equipment
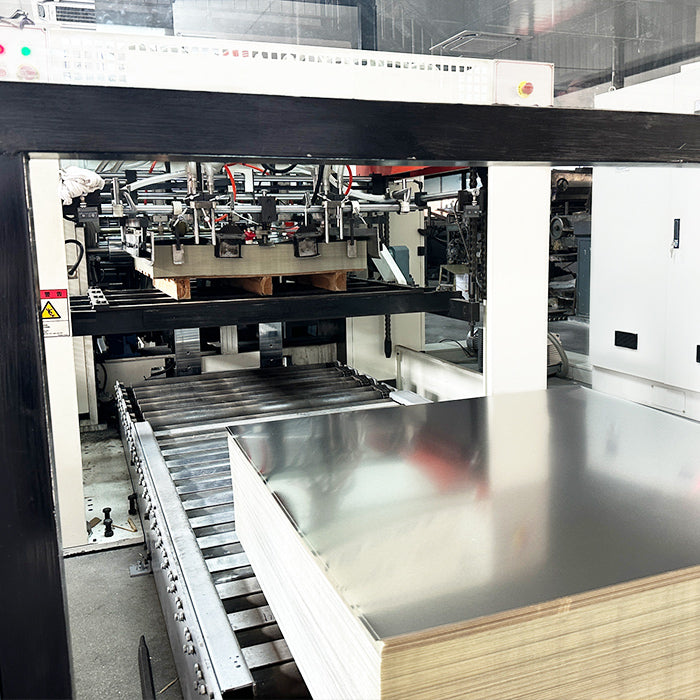
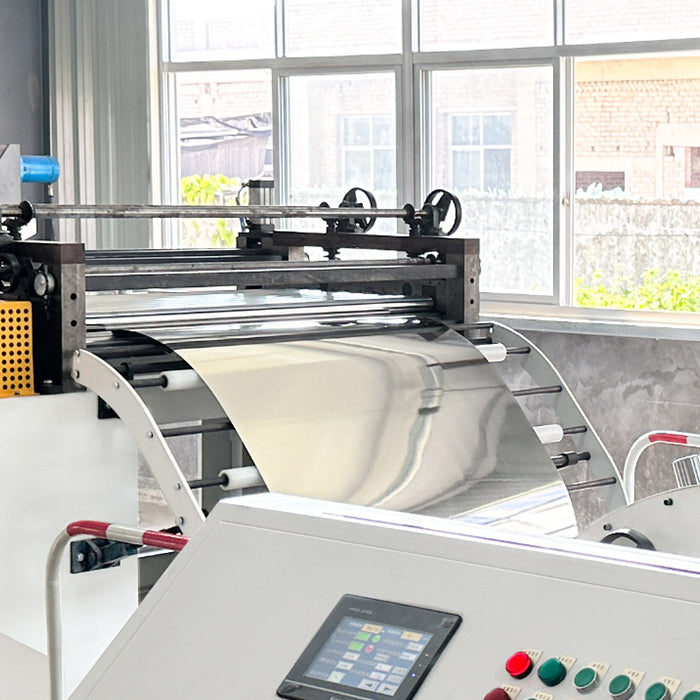
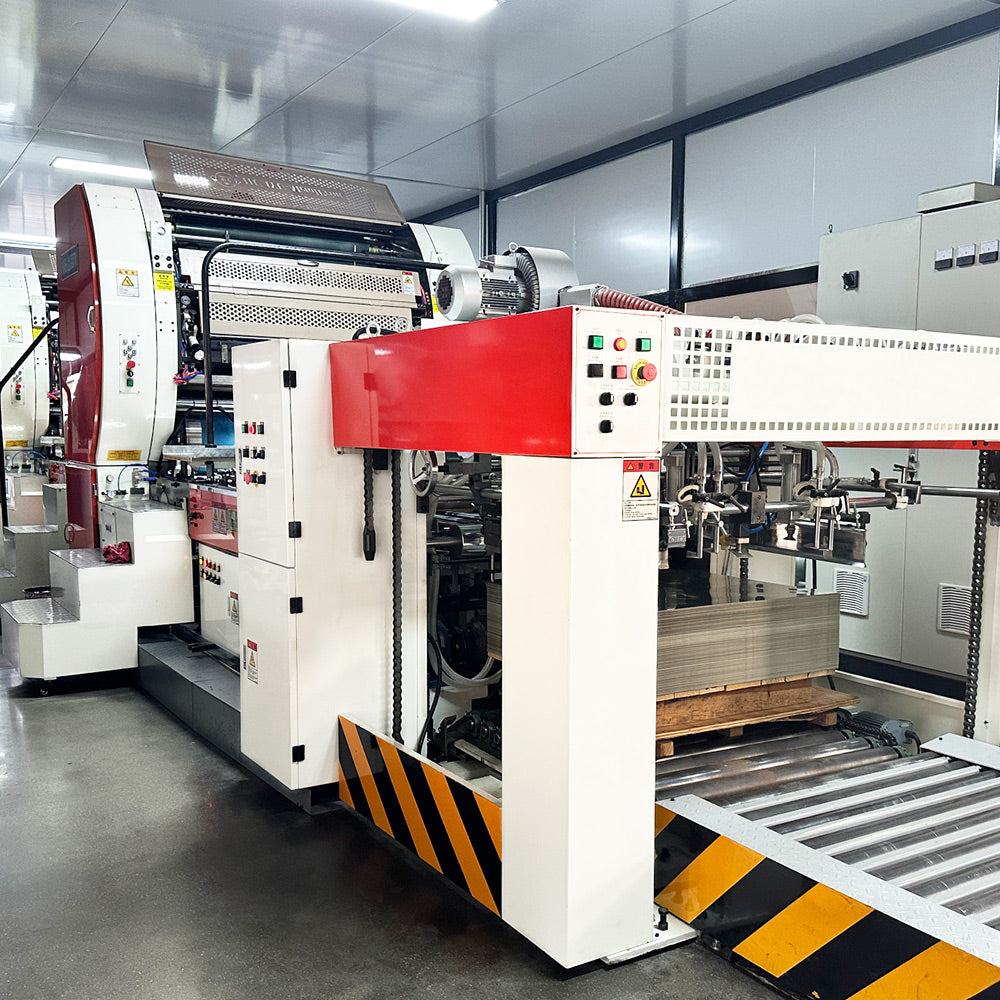
Quality Assurance Testing for Tin Can Solutions
Sterilization Testing
At Connie, we recognize and understand the significance of sterilization in our industry. We perform various sterilization tests to make sure our tin cans are secure and can protect any type of food from microbial and bacterial contamination.
We use reliable laboratory equipment to perform comprehensive and quality tests to make sure we comply well with relevant hygiene and industry standards.
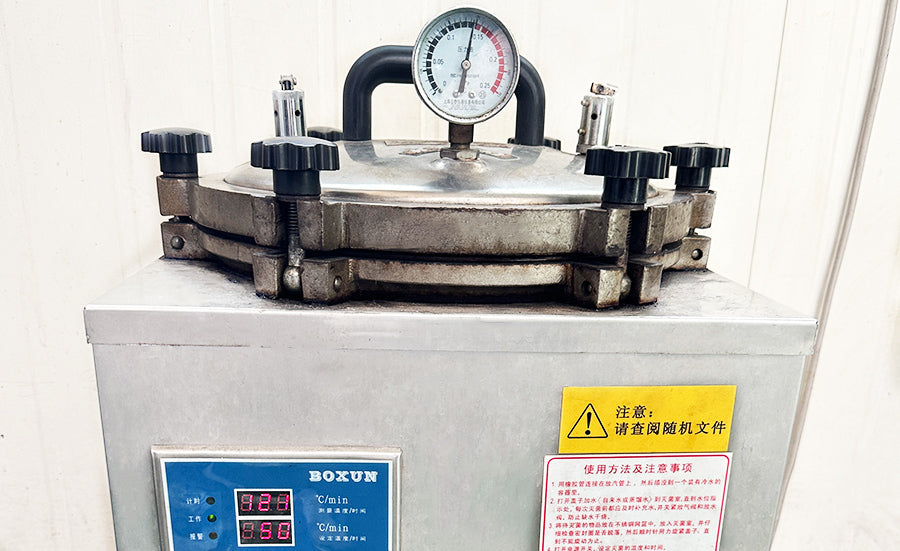
Sealing Testing
A tight seal is essential for maintaining the quality and freshness of food items. To produce airtight and seal-proof 2-piece and 3-piece tin cans, we perform detailed sealing tests.
We perform multiple tests on the seals between the bodies and lids of our cans to make sure there is no interference or leakage during the storage and transportation of food items.
We use industry-standard tests and equipment to make sure each can offer a reliable and secure seal.
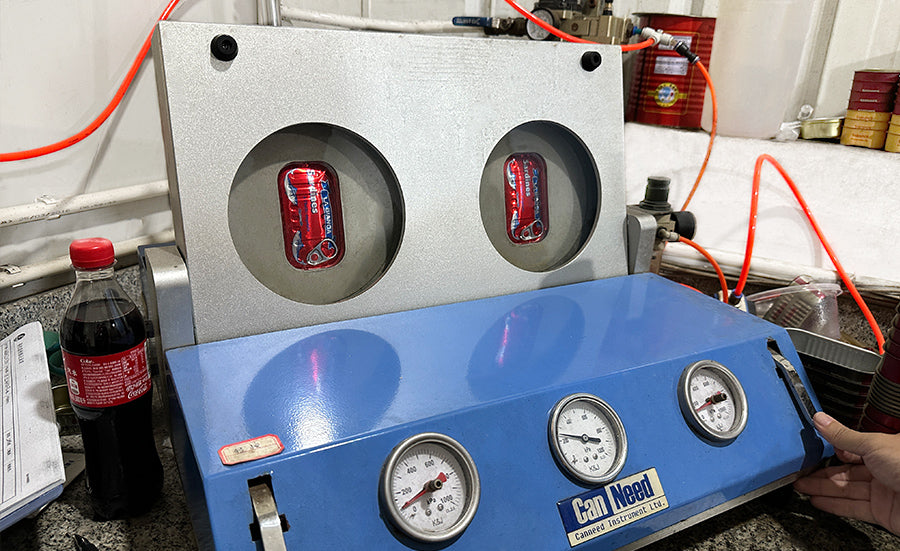
Insulation Testing
We understand that insulation performance is of utmost importance for cans that require temperature retention. At Connie, we carry out rigorous insulating testing to assess the capability of our cans to maintain the temperature of food items under various temperature conditions.
We perform tests in controlled environments to make sure our 2-piece and 3-piece tin cans give you unmatchable insulation performance, making sure that the taste and quality of stored items are never affected by temperature changes.
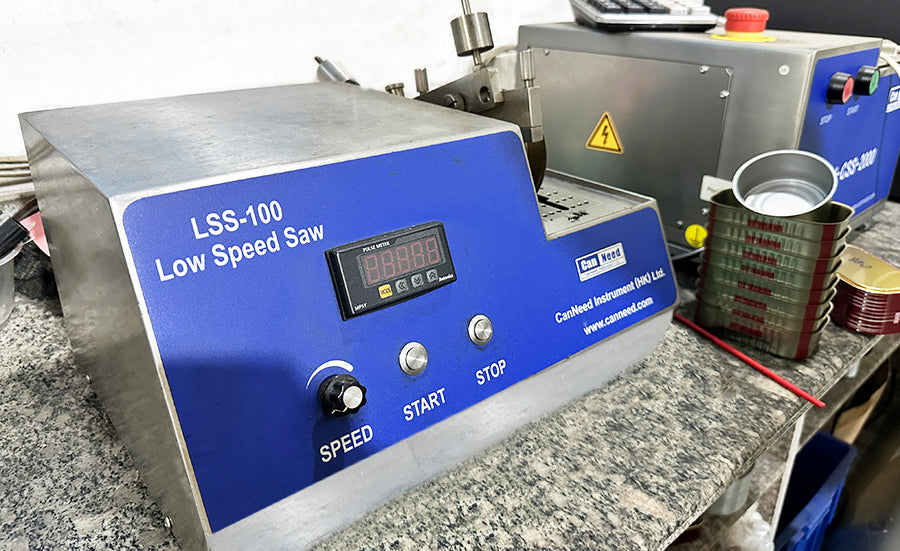
Can Data Testing
With streamlined tests, we collect and assess can data to ensure their reliability and quality. We perform a variety of detailed tests including impact resistance tests, tensile strength tests, and thickness tests to assess and ensure the resilience and durability of our custom cans during use.
Our comprehensive tests make sure that our custom tin cans can withstand the test of time and offer consistent performance.
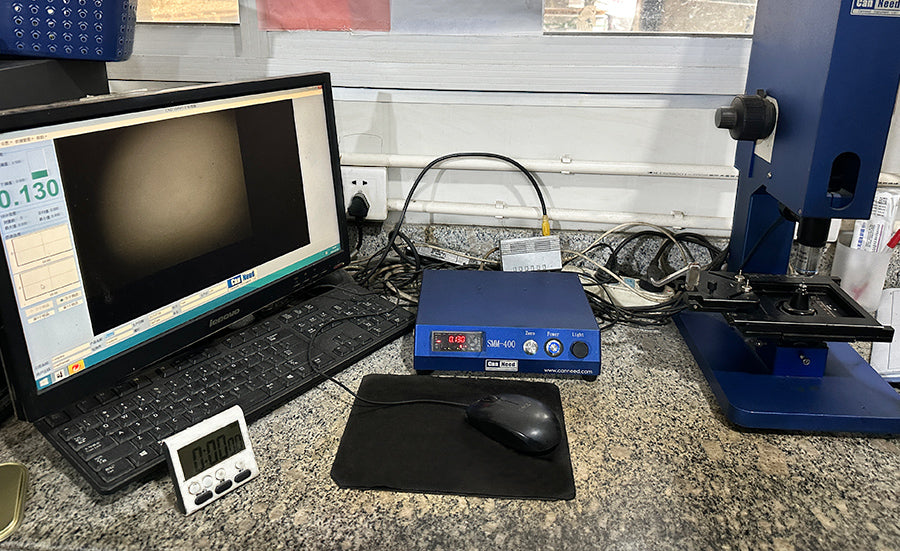
Product chain
Tinplate Coiled Iron
First of all, we melt the raw material, cast it, and then roll it into wide and thin tinplate coils. Typically, these tinplate coils are in the form of tinplate for facilitating the subsequent manufacturing process.
Tinplate Cutting
In the second step, all the tinplate coils are decently cut into the desired shapes and sizes. A variety of cutting equipment such as shears are utilized for cutting different tinplate coils into metal sheets of different sizes.
Manual Selection
Manual selection is performed for different metal sheets. The quality of these sheets is inspected by operations and any defective or damaged ones are discarded. It is important to note that only effective metal sheets are used.
Coating
The selected metal sheets are required to undergo a coating process for the improvement of their decorative properties and corrosion resistance. Another protective layer such as an organic paint of epoxy resin is applied on the surfaces of these sheets.
Printing
It is important to note that the coated metal sheets are then printed with decorative designs, texts, patterns, and brand logos as required. Usually, printing is carried out using inkjet printing or screen printing.
Can Manufacturing
Lastly, the selected metal sheets are folded for the formation of can bodies. Advanced machinery is used for performing this process and ensuring precision and stability to different can bodies.